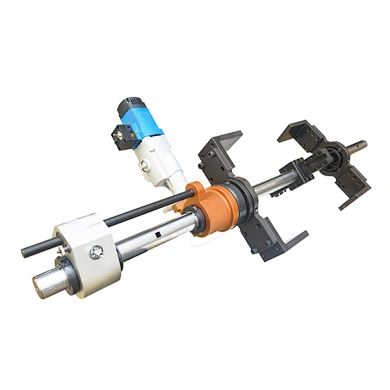
# Flange Facing Machine: Essential Tool for Precision Machining
## Introduction to Flange Facing Machines
Flange facing machines have become indispensable tools in modern industrial settings, particularly in sectors requiring high-precision machining of pipe flanges. These specialized machines are designed to restore, repair, or create perfectly flat and smooth surfaces on flange connections, ensuring optimal sealing performance in piping systems.
## How Flange Facing Machines Work
These machines operate by rotating a cutting tool across the flange face while maintaining precise control over depth and angle. The process typically involves:
- Securing the machine to the flange using chains or magnetic bases
- Adjusting the cutting tool to the desired specifications
- Rotating the cutting head to remove material evenly across the surface
- Finishing with fine cuts to achieve the required surface finish
## Key Applications in Industry
Oil and Gas Sector
In the oil and gas industry, flange facing machines are critical for maintaining pipeline integrity. They ensure proper sealing surfaces for high-pressure applications, preventing dangerous leaks in refineries, offshore platforms, and transmission systems.
Power Generation
Power plants rely on these machines to maintain steam and water piping systems. Properly faced flanges are essential for preventing energy losses and maintaining system efficiency in both conventional and nuclear power facilities.
Shipbuilding and Repair
Marine applications demand precision flange work for engine rooms, piping systems, and offshore structures. Portable flange facers are particularly valuable for on-site repairs in shipyards and at sea.
## Advantages of Modern Flange Facing Equipment
Contemporary flange facing machines offer numerous benefits over traditional machining methods:
- Portability: Many models are designed for on-site use, eliminating the need to remove piping components
- Precision: Advanced models can achieve surface finishes within 0.001″ tolerance
- Versatility: Capable of working with various materials including carbon steel, stainless steel, and exotic alloys
- Time efficiency: Dramatically reduces downtime compared to sending components to machine shops
Keyword: Flange facing machine
## Choosing the Right Flange Facing Machine
When selecting a flange facing machine, consider these factors:
Factor | Consideration |
---|---|
Flange Size Range | Ensure the machine accommodates your typical flange diameters |
Power Source | Choose between electric, pneumatic, or hydraulic models based on your work environment |
Material Compatibility | Verify the machine can handle your specific material types and hardness |
Portability Needs | Consider weight and setup requirements for field work versus shop use |
## Maintenance and Safety Considerations
Regular Maintenance
Proper care extends machine life and ensures consistent performance. Key maintenance tasks include:
- Regular lubrication of moving parts
- Inspection and replacement of cutting tools
- Cleaning of chips and debris after each use
- Periodic calibration checks
Safety Protocols
Always follow these safety guidelines when operating flange facing equipment:
- Wear appropriate PPE including safety glasses and gloves
- Secure the workpiece properly before starting
- Follow lockout/tagout procedures during maintenance
<li